Essential Pipe Welding Methods and How to Select a Reliable Service
Discover key pipe welding techniques including TIG, MIG, and flux-cored methods, and learn effective tips for selecting reliable welding services. Ensure strong, durable, and safe pipe connections for construction, industrial, and residential projects by understanding the differences in welding technology and choosing experienced professionals. This guide highlights essential industry standards, safety protocols, and quality assurance measures to help you make informed decisions for your pipe welding needs.
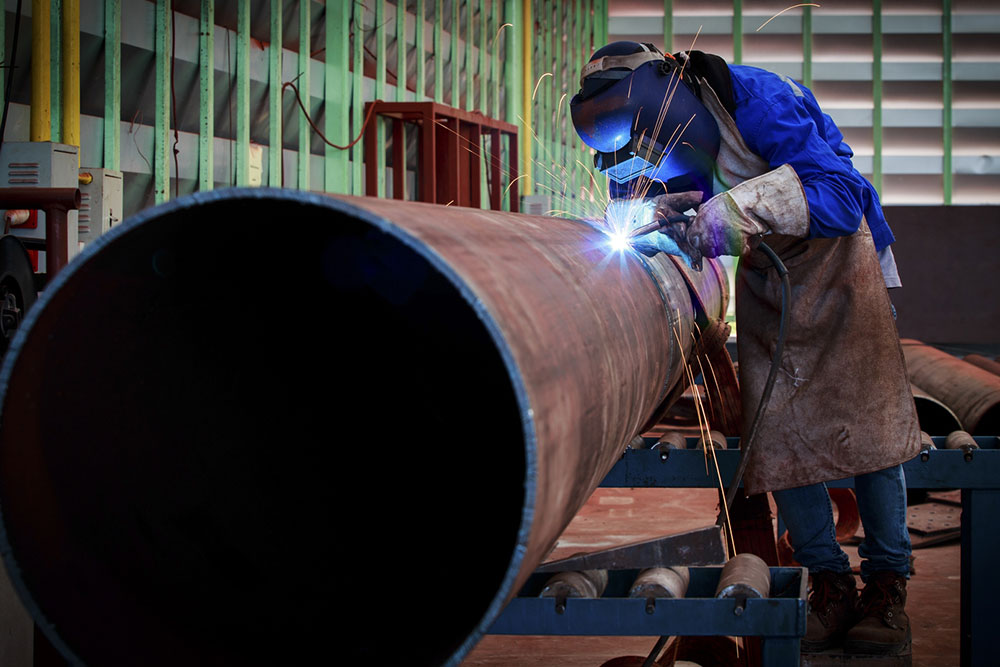
Essential Pipe Welding Methods and How to Select a Reliable Service
Joining metal pipes seamlessly is crucial in numerous industries, from oil and gas transmission to residential plumbing and climate control systems. High-quality pipe welding ensures durable and safe connections that support project longevity. Choosing a proficient welding provider is vital, as their expertise impacts the success and safety of the work. Skilled welders utilize various techniques tailored to the material and project requirements, emphasizing precision and reliability.
Popular Pipe Welding Techniques
Wielding different methods allows welders to adapt to diverse pipe materials and thicknesses.
1. TIG Welding
Also called Gas Tungsten Arc Welding (GTAW), TIG welding offers high precision and clean results. It uses a non-consumable tungsten electrode to heat the pipe edges, which are then joined with a filler rod. This technique is ideal for stainless steel, aluminum, and non-ferrous metals, providing strong, precise welds.
2. MIG Welding
Metal Inert Gas (MIG) welding employs a continuously fed filler wire electrode that melts to join pipes quickly. It suits both ferrous and non-ferrous metals and is favored for its speed. However, it may not always match TIG’s weld quality, especially in critical projects requiring meticulous results.
3. Stick Welding
Also known as Shielded Metal Arc Welding (SMAW), this method uses flux-coated electrodes. The flux shields the weld pool from contamination, making it suitable mainly for carbon steel pipes. It's a cost-effective technique often employed in construction and repair tasks.
4. Flux-Cored Arc Welding (FCAW)
A variation of MIG welding, FCAW uses a special flux core wire that provides flux and protection during welding. It is faster and better suited for thicker pipes and outdoor environments, offering efficiency and durability.
5. Submerged Arc Welding (SAW)
This industrial technique employs a granular flux layer that covers the weld area, preventing contamination and ensuring high-quality welds on thick-metal pipes. Commonly used in large-scale pipe fabrication, it offers consistency and strength.
How to Pick the Right Pipe Welding Service
Choosing the right pipe welding contractor is essential for project success. Prioritize experience, certifications, and reputation. Verifying quality standards, safety practices, and customer reviews helps ensure you select a dependable provider. Skilled professionals with proper equipment can deliver strong, reliable welds that withstand environmental stresses. Always confirm the service provider adheres to safety regulations and uses top-grade materials for optimal results.
Key Tips for Selecting a Welding Provider
Research multiple providers to compare their expertise, reviews, and pricing before making a decision.
Ensure technical competence with certified technicians experienced in pipe welding.
Assess quality assurance by checking past work, guarantees, and client feedback.
Verify safety protocols to ensure they follow proper safety standards and regulations.
Reliable pipe welding significantly influences the safety and durability of your project. Investing time in selecting an experienced, certified, and safety-conscious service provider is crucial to achieving the best results.