Essential Guide to Preventive Maintenance Software for Equipment Care
Discover the importance of preventive maintenance software for industrial equipment. Learn how it simplifies maintenance schedules, reduces errors, and boosts equipment lifespan. Find tips on choosing the right system for your business to ensure safety, efficiency, and cost savings.
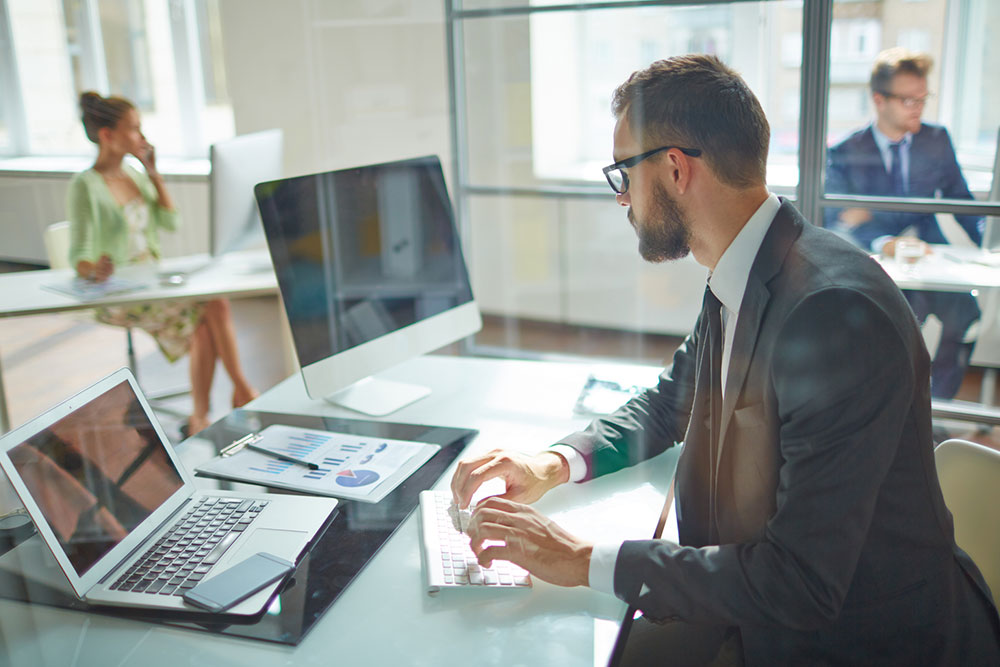
Essential Guide to Preventive Maintenance Software for Equipment Care
Effective equipment management is vital for businesses to maintain smooth operations, especially in manufacturing and industrial settings. Unscheduled machinery failures can cause costly delays and hamper productivity. Implementing preventive maintenance solutions helps ensure machinery functions optimally and reduces repair expenses. Preventive maintenance software automates scheduling, alerts, and record-keeping, enabling organizations to stay ahead of potential issues and extend equipment lifespan.
Understanding preventive maintenance involves regularly servicing machines to prevent breakdowns and unnecessary repairs, saving costs and improving operational efficiency.
Managing maintenance manually in large factories can be overwhelming, with staff needing to monitor each machine’s schedule. To simplify this, many companies turn to preventive maintenance software that automates alerts and keeps detailed maintenance records.
Advantages of using maintenance management software
Reduction in manual effort: Automated systems generate and update maintenance logs and notify staff about upcoming tasks, freeing up resources and boosting productivity.
Minimized errors: With multiple machines, manual oversight can lead to overlooked maintenance—software ensures timely reminders to prevent long-term damage.
Proactive maintenance helps avoid costly repairs and operational downtime, which is why many organizations invest in dedicated software. This technology tracks deadlines and cycles, helping maintain machinery effectively.
Additional benefits include:
Enhanced customer satisfaction: Well-maintained equipment in manufacturing reduces product delays, leading to happier clients.
Extended asset lifespan: Regular upkeep increases equipment durability by prompting timely servicing.
Consistent production flows: Properly maintained machinery operates more efficiently, cutting supply chain disruptions.
Improved safety: Preventative checks diminish risks like leaks or equipment failures that could harm workers or the environment.
Better resource utilization: Reducing repair costs allows reinvestment into advanced machinery or expansion plans.
Guidelines for selecting the right maintenance software
Assess the provider’s reputation: Choose a vendor with proven experience and positive reviews in equipment maintenance solutions. Verify their credibility and seek feedback from other users.
Check software features: Ensure the system offers essential functionalities like enterprise asset management, automation of preventive tasks, and comprehensive history tracking. Extra features like barcode integration or multi-system compatibility are advantageous.
Budget and trial options: Understand the pricing structure—ranging from $20 to $80 monthly for small businesses up to $150–$300 for enterprise solutions. Look for free trials to evaluate suitability before committing.
Prioritize customer support: Reliable vendors offer ongoing support through various channels like 24/7 chat, helplines, and dedicated email assistance. After-sales service is crucial for seamless implementation and problem-solving.