Premium Ready Mix Concrete: Costs, Suppliers, and Key Benefits
Discover the advantages, types, and costs of ready mix concrete (RMC). Produced in specialized factories with strict quality standards, RMC ensures high durability and fast project completion. Learn about different types like transit, shrink, and central-mixed concrete, along with their unique features. While more expensive than on-site mixing, RMC offers reduced cement usage, minimal errors, and timely delivery, making it an ideal choice for large-scale construction projects seeking reliability and efficiency.
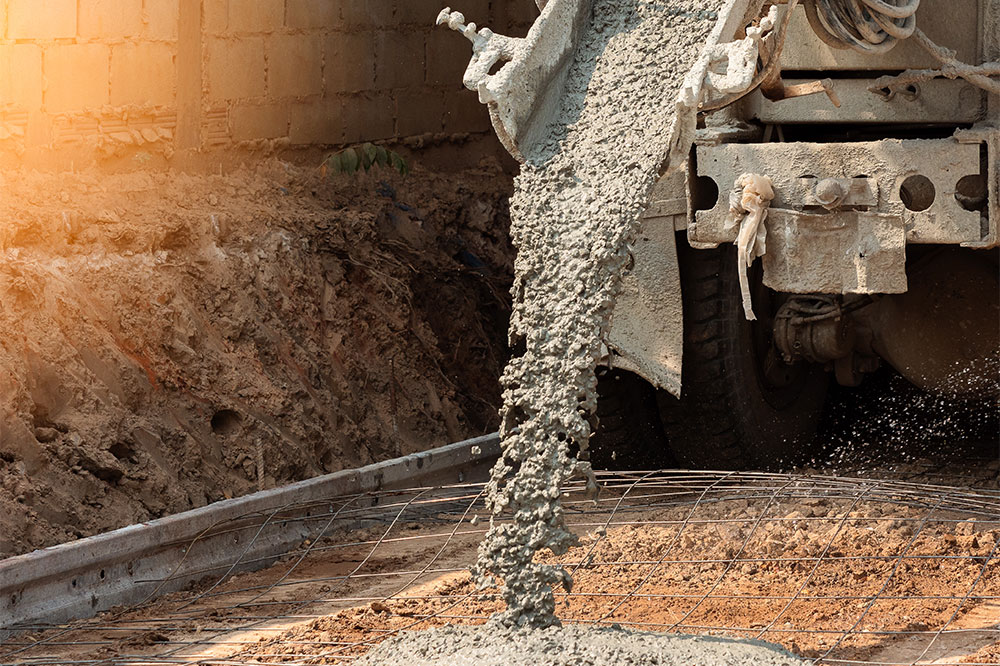
Premium Ready Mix Concrete: Costs, Suppliers, and Key Benefits
Ready mix concrete, often called RMC, is produced in specialized factories using precise mix formulas. It is then transported to construction sites via trucks equipped with transit mixers. While this process incurs higher costs compared to on-site mixing, the advantages it offers—such as superior quality and faster construction—are significant.
Below are some advantages of ready-mix concrete and its various types.
Advantages of Ready Mix Concrete
Enhanced Quality
Manufacturing plants equipped with advanced machinery ensure that ready-mix concrete is of consistently high quality. Strict quality control, testing, and standardized procedures enhance the durability and reliability of the concrete compared to traditional site-mixed variants.
Rapid Production Capacity
Automated, mechanized production at manufacturing facilities allows for large-scale and efficient concrete output. While on-site mixers produce about 4-5 cubic meters per hour, plants can generate 30-60 cubic meters per hour, ensuring ample supply for large projects.
Reduced Cement Consumption
The precise mixing process and use of admixtures decrease the amount of cement needed by approximately 10-12%, resulting in cost savings and environmental benefits. Proper proportions and quality control help optimize material usage.
Minimal Human Error
Automated processes involving exact calculations significantly lower human intervention, leading to fewer mistakes. This results in more durable structures and reduced lifecycle maintenance costs.
On-Time Delivery
Manufacturers follow strict protocols for measuring and batching, ensuring timely supply whether small or large quantities are needed. This reliable delivery is vital for project schedules.
Common Types of Ready Mix Concrete
There are three main categories: transit-mixed, shrink-mixed, and central-mixed concrete.
Transit-Mixed Concrete
Also called dry-batch concrete, this type involves loading all ingredients directly into the truck mixer, which then revolves at high speed during loading and slows during transit. It has three variations: mixed at site, mixed during transit, and mixed in the yard.
Mixed at Site
The mixer rotates slowly during transport, then speeds up to discharge at the destination.
Mixed During Transit
The mixer rotates at medium speed during transit, then slows before discharge.
Mixed in Yard
The concrete is partially mixed at the factory, then finished in transit.
Shrink-Mixed Concrete
This combines partial mixing at the plant with additional mixing in transit, based on calculated requirements after testing.
Central-Mixed Concrete
Also known as central batching or pre-mix, all ingredients are thoroughly mixed before loading into the truck, which acts only as an agitator during transit to prevent separation.
Note:
The information shared here is for general understanding and research purposes. While we strive to provide accurate data, readers should verify specifics with local suppliers or experts for their projects. Our platform does not guarantee the completeness or accuracy of all information. Offers and schemes mentioned may vary across regions and providers.